Are you looking to optimize your company’s production process and unlock its true potential? Liquid capsule filling equipment may be the answer you’ve been searching for. By investing in this cutting-edge technology, you can streamline your operations, increase efficiency, and ultimately drive profitability.
In this blog post, we will explore the world of liquid capsule filling technology, its business benefits, key features to look for in machines, challenges that may arise, compliance and quality control considerations, success stories of implementation through case studies, and future trends in the industry.
Understanding Liquid Capsule Filling Technology
Liquid capsule filling technology represents a sophisticated method pivotal in delivering liquid-based formulations into capsules with high precision. This technique is crucial across various sectors, notably in pharmaceutical, nutraceutical, and cosmetic industries, where the encapsulation of liquids requires meticulous accuracy to maintain the integrity and efficacy of the products.
The process encompasses several critical stages, starting from the preparation of capsules, which involves their separation and orientation, to the precise filling phase where the liquid formulation is deposited into the capsules. Following the filling stage, the capsules are sealed to protect the contents and ensure longevity. Finally, the capsules are ejected, ready for the next phase of packaging or further processing.
The core of this technology lies in its ability to handle a diverse range of liquid formulations, from viscous to aqueous solutions, with the versatility to accommodate various capsule sizes and materials. This adaptability makes it an indispensable asset for manufacturers looking to diversify their product lines or improve existing products.
The precision in dosing ensures that each capsule contains an exact amount of the liquid formulation, critical for ensuring dosage accuracy, a fundamental aspect especially in the pharmaceutical field where dosing precision can significantly impact the therapeutic effectiveness of a medication. Through its complex yet efficient processes, liquid capsule filling technology stands as a cornerstone for industries aiming at innovation and quality in liquid encapsulation.
The Business Benefits of Investing in Liquid Capsule Filling Equipment
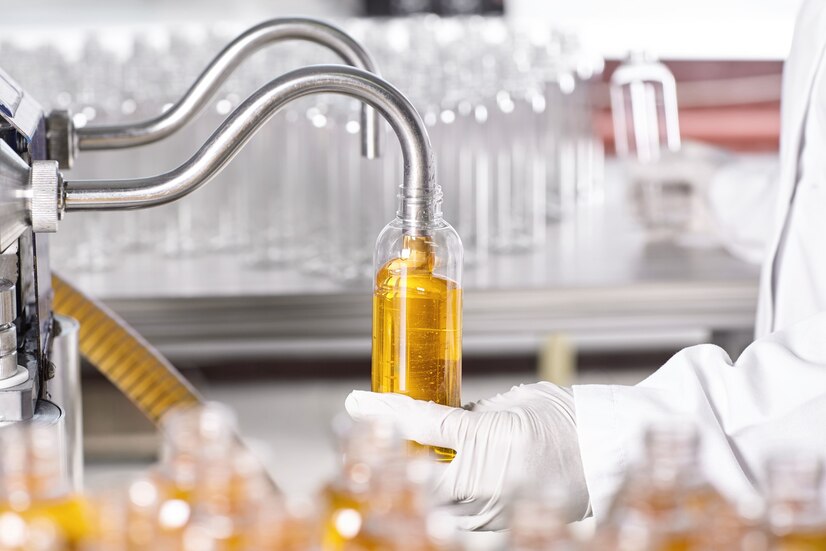
Embracing liquid capsule filling equipment propels companies into a realm of enhanced productivity and operational efficacy. This pivotal investment opens doors to accelerated production cycles, enabling businesses to swiftly respond to market demands and expand their market footprint. Notably, the automation integrated into these systems diminishes the reliance on intensive manual labor, thereby reducing labor costs and minimizing human error.
The consistency in capsule filling achieved through automated precision also elevates product quality, fostering customer trust and loyalty. Furthermore, the adaptability of these machines to accommodate a myriad of liquid formulations and capsule sizes allows for a broader product offering, catering to diverse customer needs and tapping into new market segments.
Enhanced quality control mechanisms inherent in these systems ensure compliance with rigorous industry standards, safeguarding against costly recalls and reinforcing the company’s reputation for reliability. In essence, the strategic acquisition of liquid capsule filling equipment marks a transformative step towards achieving operational excellence and securing a competitive edge in the marketplace.
Key Features to Look for in Liquid Capsule Filling Machines
Selecting the ideal liquid capsule filling machine requires attention to several critical features that can significantly enhance your production process. First and foremost, prioritize machines with high-speed capabilities to ensure that your production meets demand efficiently. Additionally, an accurate dosing mechanism is paramount. This feature guarantees that each capsule is filled with a precise amount of liquid, crucial for maintaining product consistency and adhering to stringent dosage requirements.
Another essential aspect is the user interface. Opt for machines that offer an intuitive, easy-to-navigate interface, facilitating seamless operation and reducing the learning curve for operators. The versatility of the machine is also a key consideration; it should be capable of handling a diverse array of liquid formulations ranging from thick gels to thin oils, as well as accommodating different capsule sizes and types, thus providing the flexibility to expand your product line and meet various market needs.
Compliance with industry standards and regulations is non-negotiable. Ensure that the equipment meets all relevant safety and quality specifications to maintain the highest levels of product integrity and safety. Lastly, seek out machines that are designed with robust maintenance and troubleshooting support. This includes accessible customer service from the manufacturer, availability of spare parts, and detailed documentation, ensuring that any potential operational hiccups can be swiftly addressed, minimizing downtime and sustaining productivity.
Overcoming Challenges in Liquid Capsule Filling
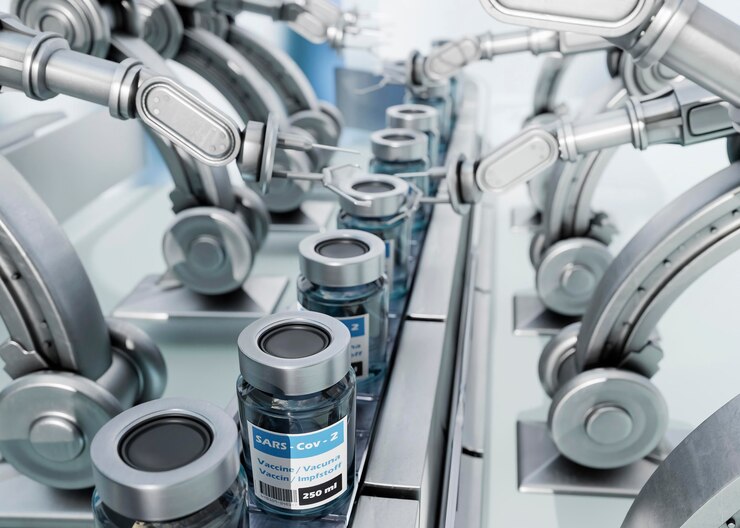
Integrating liquid capsule filling systems into a company’s production line comes with its unique set of challenges, such as mastering complex equipment maintenance, streamlining operator training, and efficiently diagnosing and resolving technical issues. These obstacles can initially seem daunting, but they are not insurmountable.
A proactive strategy involves fostering a strong partnership with the equipment manufacturer. This relationship is key to accessing specialized training and support, which can significantly ease the learning curve for operators and maintenance staff. Additionally, companies should allocate resources to develop in-house expertise, enabling quick responses to operational challenges and reducing downtime.
Implementing a robust system for logging and analyzing errors can lead to continuous improvement in handling the machinery. Regularly scheduled maintenance checks, guided by the manufacturer’s recommendations, will preempt many common technical problems, ensuring the longevity and reliability of the equipment. By taking these steps, businesses can navigate the complexities of liquid capsule filling technology and harness its full potential for their operations.
Compliance and Quality Control in Liquid Capsule Filling
In the realm of liquid capsule filling, the imperatives of compliance and quality control stand as pillars ensuring the integrity and success of production operations. Adhering to stringent regulatory requirements, dictated by bodies such as the FDA in the pharmaceutical sector, is non-negotiable. These regulations encompass the entirety of the manufacturing process, from raw material sourcing to the final inspection of filled capsules, mandating meticulous documentation and traceability at every step.
Implementing rigorous quality control protocols is fundamental to not only meeting these regulatory standards but also to fostering consumer trust in the safety and efficacy of the finished products. This entails the deployment of advanced inspection and testing methodologies throughout the production cycle. Techniques such as in-line weight checks and visual inspection systems play a critical role in identifying and rectifying deviations in real-time, ensuring uniformity and accuracy in the filled capsules.
Moreover, embracing a culture of continuous improvement and quality assurance beyond the basic compliance requirements can propel a company to industry leadership. Investing in staff training, embracing technological advancements in quality control, and engaging in regular audits and reviews of compliance practices help in maintaining an edge in operational excellence and product reliability.
Case Studies: Success Stories of Liquid Capsule Filling Implementation
The transformative power of liquid capsule filling technology shines brightly in the stories of companies who’ve embraced it. A pharmaceutical giant, facing challenges with production bottlenecks and escalating costs, turned to advanced liquid capsule filling equipment. The result? A staggering 40% increase in production efficiency and a reduction in operational costs by 25%, dramatically boosting their market competitiveness and profitability.
Another notable success story comes from a nutraceutical company. They sought to diversify their product line but were hindered by their existing equipment’s limitations. After integrating versatile liquid capsule filling machinery capable of handling various formulations and capsule sizes, they not only expanded their product range but also improved product quality. This strategic move attracted a wider customer base and led to a 35% surge in sales within the first year of implementation.
These case studies underscore the profound impact that investing in the right liquid capsule filling equipment can have. By addressing specific production challenges and leveraging the technology’s versatility and precision, companies across different industries have not only solved immediate problems but also positioned themselves for sustained growth and innovation.
Future Trends in Liquid Capsule Filling Technology
The horizon of liquid capsule filling technology is marked by groundbreaking advancements poised to redefine operational efficiencies and product quality. Robotic automation emerges as a game-changer, offering unprecedented precision and consistency in the filling process while dramatically reducing human error and labor costs. This shift not only enhances production capacity but also introduces a new level of safety and cleanliness, crucial for industries with stringent regulatory standards.
Smart sensors represent another leap forward, equipping machines with the ability to monitor and adjust the filling process in real-time. This adaptability ensures optimal accuracy in dosage and minimizes waste, directly impacting profitability and sustainability. The integration of data analytics into liquid capsule filling operations opens up avenues for predictive maintenance and process optimization. By analyzing performance data, companies can anticipate equipment failures before they occur, schedule maintenance more efficiently, and adjust production parameters for enhanced output.
Additionally, the push towards customization and flexibility in manufacturing is leading to the development of machines capable of easily switching between different capsule sizes and types without significant downtime. This adaptability allows companies to respond more dynamically to market trends and consumer demands. As we look to the future, the convergence of these technologies promises not only to elevate the capabilities of liquid capsule filling equipment but also to empower companies to navigate the complexities of modern manufacturing landscapes with greater agility and confidence.
Also Read:
- Cristiano Ronaldo – Networth
- 3 Best Chicken Rice In Singapore
- Adobe Premiere Pro: All you need to know
- Apple Final Cut Pro: All You Need To Know
- Popular Dog-Friendly Eateries In The Area Of Brighton